

Dimensional Engineering and Tolerancing
Optimize tolerances, GD&T, assembly sequence, and assembly processes through design iterations and analysis.
Dimensional analysis is the exact way to optimize your designs through iterative changes and deep analysis of your assembly. It allows you to ensure your final product. Its outputs support your product from the concept phase to series production (interface requirements, assembly concepts, reference systems & tolerances). Its contribution to your product is mentioned briefly below.
-
Manufacturing cost reduction by tolerance optimization.
-
Scrap rate reduction.
-
Ensuring the installation of components and parts.
-
Aerodynamic performance increases.
-
Prevision of assembly problems during the design phase.
As Precision Machining Consultancy, we are responsible for developing, documenting, and maintaining dimensional requirements for components and assemblies, including datum definition, tolerances, and measurement points. We are defining and documenting datum and locator schemes at the part and sub-assembly level, running both 1D and 3D tolerance stacks, using statistical data to make design improvement recommendations, and tracking the implementation of these recommendations into the designs to ensure the product conforms to the build objectives.
We are working with the manufacturing and assembly teams to ensure that the design is optimized and the method of manufacture and assembly aligns with the design requirements. We work with the quality organization to align and agree on check gauges and measurement techniques. As a part of dimensional engineering, we help define the tools and methods used to generate the statistical data needed to influence and improve the design.
All in all, we support the multidisciplinary work between engineering, the metrology department, and suppliers to achieve the most effective dimensional control scheme including the definition of Key Characteristics (“As precise as necessary, as imprecise as possible”).
Steps

Links and Assembly
Definition of how to restrict 6 DoF of parts and components during the assembly phase.
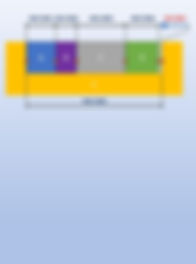
1-D Stackup Study
One dimensional tolerance stack-up analaysis. Simple and efficient way to start.
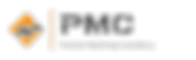
3-D Dimensional Variation Analysis
Having results by taking rotational impacts into account in 3 dimensional space

Evaluation of Results
Final decision made by utilizing Monte Carlo simulation and Statistical methods.
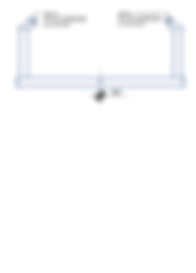
Providing GD&T and Design Gaps
Describe the key features of the service and how users can benefit from it.
Abilities
-
In-depth knowledge of GD&T and ASME Y14.5-2009 and ISO GPS. Guide Datum selections, Measurements, and GD&T application by ASME standards.
-
Executing three-dimensional variation analysis.
-
Provide Input to manufacturing assembly sequence and assembly concept decision-making process
-
Expertise in manufacturing technologies, processes, and achievable tolerances.
-
Familiar with inspection equipment (CMM, Check fixture, FARO, Laser Tracker, etc.).
-
In-depth knowledge of Key Characteristics and Tolerancing rules in the whole aircraft development process.
-
Ability to analyze and break down dimensional data to identify the source of problems (Sub assembly, Tooling, Supplier part, etc).
-
Monte Carlo simulation, and RSS statistical tolerance analysis.
-
Familiarity with statistical control concepts such as Cp/Cpk, and Pp/Ppk.
-
Benefitting from sensitivity analysis (GeoFactor).
-
Provide expertise on GD&T best practices and closely work with Quality and Design engineers to make sure that datum schemes and tolerances are accurate for the form, fit, and function of the assemblies